Теплообменник – эффективное устройство для передачи тепловой энергии без смешивания потоков носителей с различным температурным режимом. Ввод в эксплуатацию такого прибора требует полной предварительной проверки на герметичность и отсутствие дефектов.
Правильно проведенная опрессовка теплообменника обеспечит продуктивную и безопасную работу всего оборудования.
Что такое опрессовка
Заключительным этапом установки любого теплообменника является тестирование на прочность. Для этого используется опрессовка – проверка целостности прибора с помощью гидравлического давления. В процессе испытаний исследуется внутренний и внешний контуры.
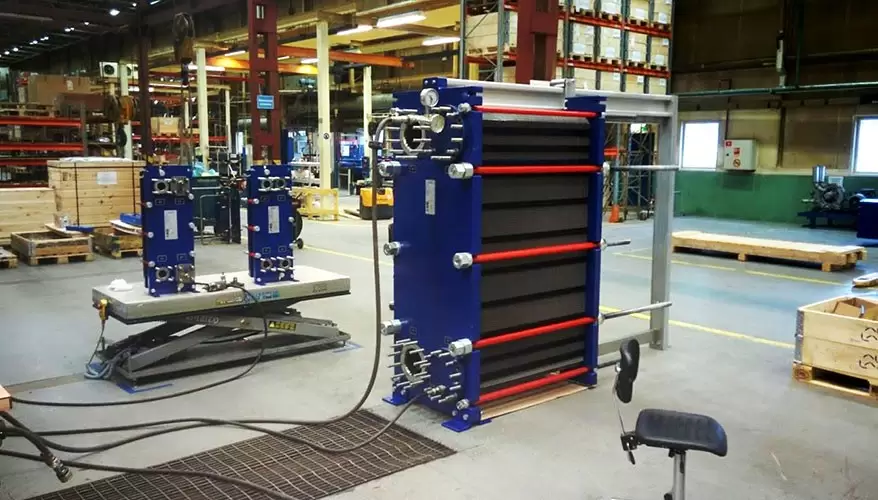
Испытание оборудования
Испытания каждой части теплообменника проводятся поочередно. Изначально гидравлический поток подается в один контур. При этом вторая сторона находится под атмосферным давлением. Тестирование другого контура осуществляется аналогичным способом.
Процесс длится не более 15 минут. Давление в теплообменном устройстве должно быть выше стандартного рабочего и не превосходить максимальные заводские показатели прибора.
Такие испытания позволяют избежать протечек во время запуска и работы. Также с помощью опрессовки можно предварительно определить рабочее состояние теплообменника.
Когда необходима опрессовка
Первое тестирование теплообменника посредством гидравлического давления проводится при установке его в систему. Такой этап обязательный при введении в эксплуатацию устройства. В дальнейшем опрессовка выполняется в ряде других случаев:
- запуск оборудования после длительного отключения;
- проведение ремонтных работ прибора;
- обновление трубопровода;
- монтаж инженерных сооружений для подачи воды;
- замена стояков.
Любое вмешательство в систему, с которой связан теплообменник, требует опрессовки. Это позволит избежать аварийных ситуаций и обеспечит качественный рабочий процесс на долгое время.
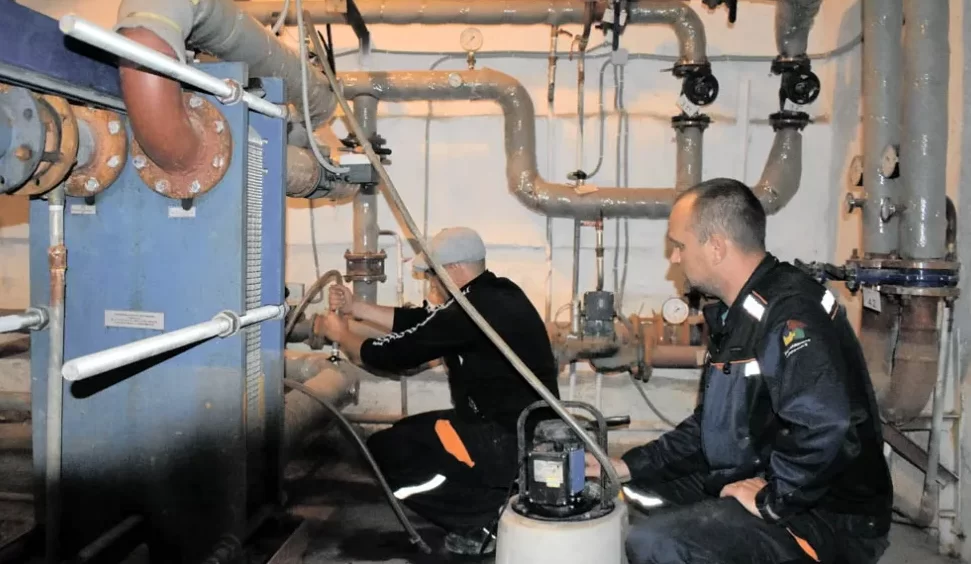
Процесс проверки герметичности теплообменника
Этапы проведения опрессовки
Для испытания теплообменника используются специальные гидравлические компрессоры с ручным или электрическим приводом. Такое оборудование позволяет создать в контуре прибора необходимое давление.
Процесс не составляет особой сложности. Для проведения тестирования на прочность теплообменного устройства необходимо:
- С помощью воды и реагентов удалить все загрязнения в приборе и системе трубопроводов.
- Подключить компрессор к первому контуру теплообменника и наполнить его жидкостью до полного устранения воздуха. Для этого в системе должен быть предусмотрен специальный штуцер (спускник).
- Плавно повысить гидравлическое давление до максимального уровня. Через 10–15 минут снизить его до расчетных параметров. Осмотреть все швы, соединения на наличие протечек.
- Таким же образом проводится испытание второго контура.
- После опрессовки всю жидкость из оборудования необходимо удалить, а полость осушить. Такие действия позволят защитить устройство от коррозии.
Чтобы избежать появления влаги на корпусе теплообменника, рекомендуется следить за разницей температуры воздуха и поверхности прибора. При успешном тестировании не должно быть разрывов на сварных швах, признаков деформации корпуса прибора и всех соединений.
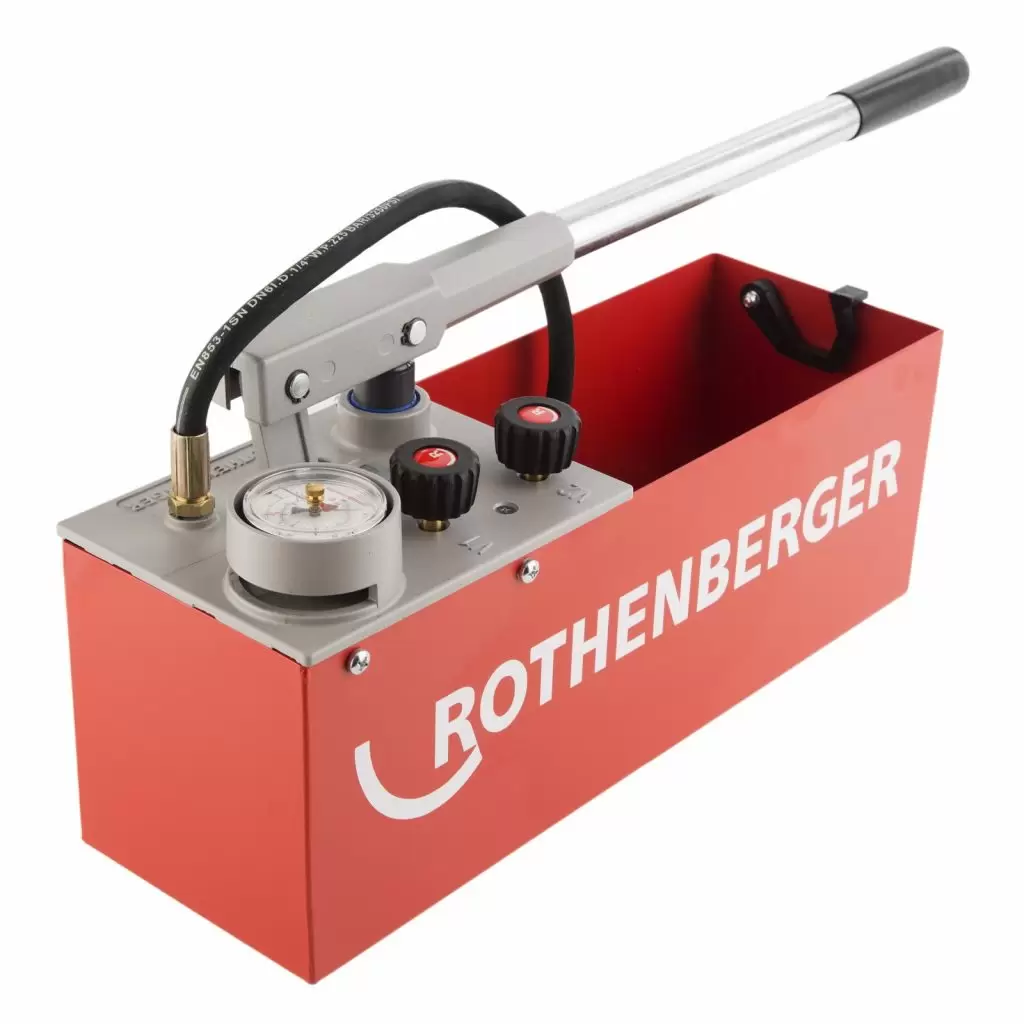
В конструкции пластинчатого теплообменника материал внутренних деталей иногда подвергается коррозийному воздействию и осаждению налета. Поэтому нужно использовать для тестирования жидкость без механических примесей и большого количества хлоридов.
Необходимость опрессовки теплообменника очевидна. С помощью гидравлической проверки на прочность можно устранить все неисправности еще до запуска системы и избежать аварийных ситуаций.